DID YOU KNOW…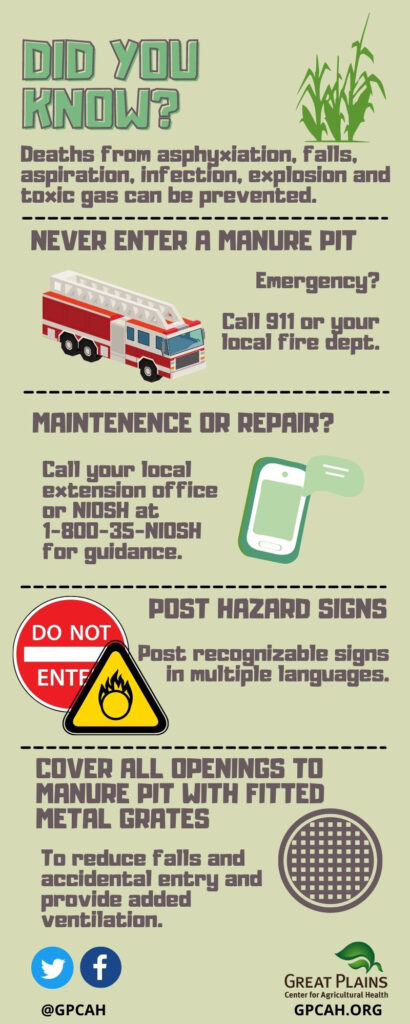
Manure gas contains a mixture of hydrogen sulfide (H2S) and methane (CH4), neither of which can be smelled when they are in high concentrations.
Inhalation of high concentrations H2S will paralyze your respiratory system, leading to asphyxiation. H2S has killed farmers and their rescuers who did not take precautions.
- You can smell H2S when it is dilute (< 1 ppm), when it is safe
- Above 10 ppm, you can no longer detect H2S by smell
- Concentrations above 50 ppm alter breathing, and over 500 ppm leads to death
If your manure pits have foam on the top, be aware that this foam contains high concentrations of methane (CH4). If you knock down that foam, you can release methane from the foam, which can result in explosive environments.
- Methane is lighter than air, and breaking foam (falling feed, wash water, pit agitation) will release methane
- Ignition sources in the building may ignite methane, resulting in fire and explosion
It is important to recognize these hazards and take precautions prior to working with manure to prevent fatalities.
What are the risks?
Hydrogen Sulfide
Fatalities associated with manure handling make the news every year. The H2S is produced naturally when bacteria break down organic matter and is released from liquid manure and sewer sludge.
In calm air environments, such as unventilated storage tanks and pits, H2S pools near the floor as it is heavier than air, but currents generated by moving through the environment can stir this into the breathing zone of someone in these areas.
Health effects are a direct function of the concentration (ppm) inhaled:
- 2 – 20 ppm: Nausea, headache, dizziness
- 50 – 100 ppm: Altered breathing
- 100-300 ppm: Pulmonary edema
- 500-700 ppm: Collapse in 5 min, death 30-60 min
- 1000 ppm: Nearly instant death
Methane
While the risk of methane explosions is relevant only to manure storage volume that have foaming, explosions have been documented as far back as the 1960s in the upper Midwest. With methane, we are typically concerned about explosions and not inhalation hazards. Methane is a simple asphyxiant, which means for every 4% increase in methane concentration, there is a decrease of 1% or oxygen in the air.
Explosion risks are high when methane that is trapped in foam is released. Foaming manure traps methane in concentrations of 50 – 70%, which are too high to be a hazard. When the foam is broken and the methane releases into the room, it dilutes to flammable concentration (5 – 15% in air, or 50,000 to 150,000 ppm).
Since methane is “lighter than air”, it will rise out of an under-floor manure pit and fill the room at flammable concentrations. If there is an ignition source (heat from a motor, pilot lights, welding/metal cutting, faulty wiring, heater turns on…), a pocket of methane may ignite and can cause explosions, depending on concentration in the room and other ignitions sources that may be running (LP heaters).
See additional information
Dangerous Scenarios: H2S
Manure Agitation Prior to Pumping
When pumping out a manure pit, solids that settled at the bottom need to be resuspended into the liquid. This agitation releases hydrogen sulfide and other gases (ammonia, carbon dioxide, methane) into the air.
Hog producers know to remove hogs from buildings prior to agitating manure to pump out manure pits. Workers also need to stay out of buildings during and following agitation (see story here). But cattle operations, including open-walled cattle buildings with under floor manure pits and open-air manure pits (during a temperature inversion) have similar risks of generating lethal concentrations of H2S affecting both animals and workers.
Entering the Manure Pit
Lethal concentrations of H2S can be present in both full and emptied manure pits. Performing equipment maintenance and “quick entries” to retrieve equipment have resulted in many fatalities across the country and around the world.
See full investigation reports at:
- 2005 IA 024 /025 Farmer and his employee died after collapse and attempted rescue in manure storage pit
- 1994 MN 057 Waste hauling service worker dies after he collapsed in an underground manure waste pit
- 1994 MN 045 Farmer asphyxiated in manure waste pit
And recent media stories about deaths when entering manure pits include:
2021
- https://ocj.com/2021/08/manure-pit-fatalities-spur-awareness/
- https://www.dailystandard.com/archive/2021-08-11/stories/43492/three-die-in-farm-accidentv
2015
- Palo Alto County, Iowa: Son entered manure pit to make repairs, and father entered to rescue him. Both died July 25, 2015. https://www.desmoinesregister.com/story/money/agriculture/2015/07/28/iowa-father-son-die-manure-pit-fumes/30809037/
- Chippewa County, Wisconsin: Son entered manure pit to retrieve equipment, and father entered to rescue him. Both died July 2, 2015. http://www.jsonline.com/news/wisconsin/2-wisconsin-men-die-after-falling-into- manure- pit-b99532179z1-311646871.html
Any entry into a manure pit needs to be treated as a confined-space entry, which should require the use of a gas monitor to warn of dangerous concentrations prior to and throughout the entry (or a SCBA respirator to be worn) and rescue equipment, personnel and plan ready to implement should the entrant need rescue.
Rescuing a Downed Colleague
Twenty-two percent of deaths in manure handling asphyxiations were among those who attempted rescues. Seeing an unconscious family member or colleague in a manure pit generates a natural response to enter the pit for rescue. It is important to realize that the next person to enter that pit is likely to experience the same lethal concentration of H2S, and preplanning activities should help you avoid entry to conduct this rescue.
Other High-Exposure Operations
While there have been no H2S asphyxiation fatalities associated with other activities inside a hog barn, studies have identified peak concentrations that have caused personal monitors to alarm, and in some cases confirming exceeding 1000 ppm during several activities. The highest exposures for these tasks were from, when pulling manure pit plugs. See: https://pubmed.ncbi.nlm.nih.gov/14679877/, https://pubmed.ncbi.nlm.nih.gov/30893975/, https://elibrary.asabe.org/abstract.asp?aid=14099, https://www.prairieswine.com/wp-content/uploads/2020/10/Hydrogen-Sulphide-Concentration-While-Pulling-Pit-Plugs-and-Power-Washing-Rooms.pdf. Elevated H2S (above 10 ppm) may also alarm monitors to signal elevated risks during pressure washing of hog barns and when land-applying manure.
Dangerous Scenarios: Methane
Methane is generated naturally in all manure pits, but when foaming occurs in this pit, the foam traps the methane. The following scenarios are dangerous because the foam can be broken, releasing methane which dilutes in the room creating explosive atmospheres
Pressure Washing
Water enters the slats and breaks the foam underneath. Pressure washing should be done only with very low volume in the manure pit, when foam is minimal, and only when ignition sources have been eliminated.
Feed System
When feed falls through slats, it can release methane from foam. Minimize risk of feed spills.
Pumping Manure Pit
Agitation that breaks foam will release methane. Preplanning is essential to maximize ventilation, remove all ignition sources, and minimize explosion risk during pumping.
Hot Work (welding, grinding)
Heat and sparks can serve as ignition source if foaming manure breaks and releases methane.
Prevent Manure Gas Fatalities
Recognize Hazards
The first step is to make sure everyone recognizes the hazards of manure gases. Post signs to educate and warn everyone of the risks of manure gases (H2S).
Communicate the risk of foaming hazards and identify risks to everyone.
Restrict Access
No one should enter a manure pit without precautions in place. Prevent accidental entries and block entry locations to prevent entry, including signage.
Plan Ahead
Formalize procedures to implement ventilation, monitoring and equipment shutdown prior to high-risk activities. Communicate procedures and risks to workers before beginning these activities. Implement strategies throughout the high-risk activities.
Room Preparation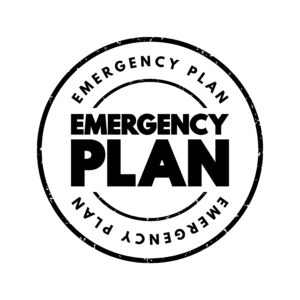
Equipment: To reduce the risk of flash fires from methane, turn off all heaters, pilot lights and electrical equipment (except ventilation fans), and make sure no other sparking/heat sources are present (e.g., no smoking). Review electrical systems to determine how to shut off and lock out systems that can generate a spark (e.g., automatic feeders and heaters). Locate the shut-off valve for propane systems to turn off prior to work with foaming manure to minimize explosion risk.
Room Ventilation: Open all air inlets to reduce static pressure of building. Maximize ventilation to exhaust air from the building, leaving it to run continuously (do not allow it to cycle on and off). In a hog barn, this ventilation rate should be not lower than 25 – 30 CFM per pig occupancy. Run room ventilation at these full levels for at least 30 minutes after any foam disturbance is completed. Continue to run pit ventilation even after the activity is stopped.
Storage Area Ventilation: Forced ventilation is needed to push clean air into an emptied manure pit/storage area before entry. Monitoring for oxygen and H2S is required prior to entry.
Other Equipment and Plans
Emergency Action Plan: Review the site’s emergency action plan to make sure they detail who and how to contact in the event of an emergency, confirm the instructions to direct emergency services to the site (specific address), where emergency shutoffs are located (and visually confirm), and any equipment needed to coordinate a rescue.
Emergency Equipment: If a worker is going to enter any manure storage area, they should be in a body harness with a safety line so they can be pulled to safety (by enough people or a winch) should a worker need extraction.
Gas Monitors: Locate and calibrate or bump test personal gas monitors for use during the high-risk activity. (See details in next section.) Plan monitor checks one to two weeks before planned high-risk activity to allow time to find a suitable replacement if the monitor is not working.
Step-by-Step Procedures
Develop and communicate procedures for high-risk activities. Example recommendations for procedure criteria are below.
Washing Barn/Changing Feed Systems with Foaming Manure Hazard
If evacuate: a. Continue ventilating, wait 15 minutees, b. Return with monitor testing every 4 ft c. Enter only when %LEL is at background
|
Hot Work with Foaming Manure Hazard
If work MUST be done, prevent any activities that might result in broken foam (NO spraying, no feeding)
If evacuate: a. Continue ventilating, wait 15 minutes, b. Return with monitor testing every 4 ft c. Enter only when %LEL is at background
|
Pumping with Non-foaming Manure
|
Pumping with Foaming Manure Hazard
|
Emergency Plan Review
Pumping with Foaming Manure Hazard
|
Review the plan and requirements prior to initiating the high-risk activities with all personnel who are involved. Explain risks of gas exposure and rescue plan (including 911 notification responsibilities) before initiating the activity. It is suggested to communicate with local emergency responders (volunteer firefighters) regarding scheduled confined space (manure pit) entry, particularly if local responders are to be called in the event of an emergency.
Make sure everyone on the farm (including spouses) understand where they can and cannot be during these activities and what their roles are. Critical to this plan should be that NO ONE is allowed to enter a manure pit to rescue someone without having a supplied air respirator – this makes having (1) emergency responders be present OR (2) having harness, lifeline, and retraction wench to retrieve someone OR (3) both critically important to this program.
Materials to start these conversations are available at the following sites:
Click on the images for printable versions.
Use Monitors
Because we cannot sense the presence of H2S or CH4 when it is at high concentrations, we need to rely on a gas monitor to detect and alert us when we are in danger. If hydrogen sulfide (H2S) is the only concern, a single-gas (H2S) monitor is needed. If we are concerned about methane as well, however, we need to have an LEL monitor, which measures “lower explosive limit”, which often makes getting a four-gas monitor appropriate (get sensors with oxygen, LEL, H2S, and carbon monoxide as the fourth sensor, as it can be useful in grain bins, combustions equipment, or failing motors). A detailed Technical Guide on monitors is available here.
Monitor Maintenance
Gas monitors come with sensors specific to the chemicals you want to measure. They typically respond by having air with that chemical of concern come into contact with chemicals inside of the sensor (“electrochemical sensors”), which then initiates a chemical reaction that changes voltage within the sensor, which is detected and processed to show you a signal that represents the concentration of that chemical. As sensors age, the sensor has less and less of the chemicals available for this chemical reaction, which is why manufacturers indicate a shelf life for these sensors.
Every time you use this sensor, when your life depends on letting you know that the air is safe or not safe, you want to make sure the sensor still responds to the chemical. For this reason, we recommend you perform a bump test EVERY day that you use this monitor to protect someone’s life. In the case of agriculture, we do recommend that you check this sensor a few weeks prior to the time you need it, typically because if you are not using it a lot or storing it in a clean area, it might not work when you need it.
This bump test requires you to obtain a container of the gas that matches your sensor (H2S or CH4, depending on what sensor you have) and putting that gas directly on the sensor. The purpose of this is to make sure that (a) the sensor can detect the gas (at the concentration you applied) and (b) how long it takes for the sensor to respond to that concentration. You should look at the displayed concentration and look to see how the monitor signals an alarm.
If the sensor does not detect the gas you challenged it with, you need to complete a full calibration or simply order a new monitor. If the sensor took longer than 1 minute to respond to the gas, it has a limited lifespan left (but you can still use it with caution). The caution for a slow responding monitor is that the user recognizes the need to move very slowly through the space to make sure that “zero” readings really reflect no presence of the gas.
Equipment needed to complete a bump test are shown here. Bump testing handouts and videos are provided in the table below using two monitors (SGC Plus and BW Clip Real Time) and two methods for conducting bump testing (Calibration Gas or Aerosol Can Gas)
Handouts | Videos | |||
H2S Monitor Type Shown | Calibration Gas Cylinder | Aerosol Can Gas | Calibration Gas Cylinder | Aerosol Can Gas |
BW Clip Real Time | BW Cal Gas | BW Aerosol | BW Cal Gas | BW Aerosol |
SGC Plus | SGC Cal Gas | SGC Aerosol | SGC Cal Gas | SGC Aerosol |
The procedure for a multi-gas monitor is similar, but you probably want to rely on a single gas cylinder that has a mixture of gases that match your four sensors. For the four-gas monitor, you need to make decisions based on the hierarchy of responses as shown below. Your first decision is always based on oxygen reading: If there is low oxygen, (<20%), do not proceed. If Oxygen is OK (must be above 19.5%), then evaluate the LEL (flammable gas). If the LEL is 10%, you should leave the space. If it is changing at all, you really should leave (it should not be changing from zero, but at 10% you are in serious danger of it being present in the room). If oxygen is 20% and LEL is zero, then you would interpret the safety of the H2S (or CO or other hazardous gas sensors) to make your decision. In any environment, if you see numbers changing quickly, there is something going on in the environment and leaving the space makes sense to figure out what is going on outside in a safe environment. In safe environments, these numbers will not change much at all. In high-risk manure operations, if the monitor is changing, remember it may be responding much slower in the device than is happening in the air (it takes time for the signal to be processed), so go to an area with lower concentration to figure out what is going on. It might be as simple as you are standing downwind of another source of the gas, so moving is safe.
Videos and Multimedia
In addition to the training videos, above, presentations are available for you at:
- Pit Foam and Producer Safety: Hazards and Prevention of Airborne Exposures and Risks (SwineCast)
- Hydrogen Sulfide and Your Safety (SwineCast)
- Pit Foam and Producer Safety (YouTube)
Additional Information on Manure Pit Hazards
- https://www.wisfarmer.com/story/news/2021/08/20/recent-fatalities-tragic-reminder-manure-storage-dangers/8215484002/
- http://www.sustainabledairy.org/Documents/DairyCap_ManureAgitation_FactSheet_Final2.pdf
- https://www.nationalhogfarmer.com/news/air-hazards-manure-pits
Additional Information on Manure Storage Space Ventilation Example Calculations
Additional Information on Foaming Manure Hazards
- Equipment safety for agitating and pumping manure safety (Puck): https://puck.com/puck-equipment-safety-part-4-agitating-and-pumping-manure-safety/
- Step-by-step procedures for animal safety when pumping manure from deep pitted barns: https://www.canr.msu.edu/news/suggested_guidelines_for_animal_safety_when_pumping_manure_from_deep_pitted
- Step-by-step procedures for caution when dealing with foaming manure pits: https://www.canr.msu.edu/news/use_caution_when_dealing_with_foaming_manure_pits